Considerations for a Successful Cable Harness
Trevor Hendricks2024-06-11T21:12:30+00:00In a previous article, we detailed how manufacturers pick the individual components of a cable. In this article, we’re going to detail the considerations that come into play when bringing that cable into a larger assembly and working with a cable manufacturer like iRex.
Lengths and tolerances
When communicating lengths of cable it is nearly essential that OEM and cable manufacturer are on the same page as to how the cable is measured. Some OEMs measure from the front of the connector, while others measure from the rear. Along these same lines, it’s helpful to note the acceptable tolerances for the cable lengths – defining how much variance above or below the stated length is acceptable.
Splicing & splice locations
There are many ways to wire or circuit, but each method has uses and advantages, therefore it’s beneficial to think through which method is used and where it is used when designing the harness.
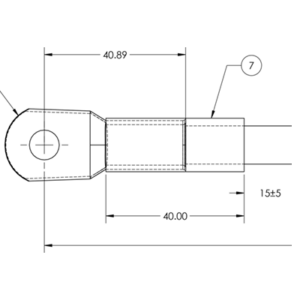
Wire color and labeling
It is common for OEMs to use specific wire colors to denote specific circuits. It’s important to list these colors out alongside any text that needs to be printed and labeled as well. It is also useful to think through whether any of the specified wire colors will conflict with other cables being used in the assembly.
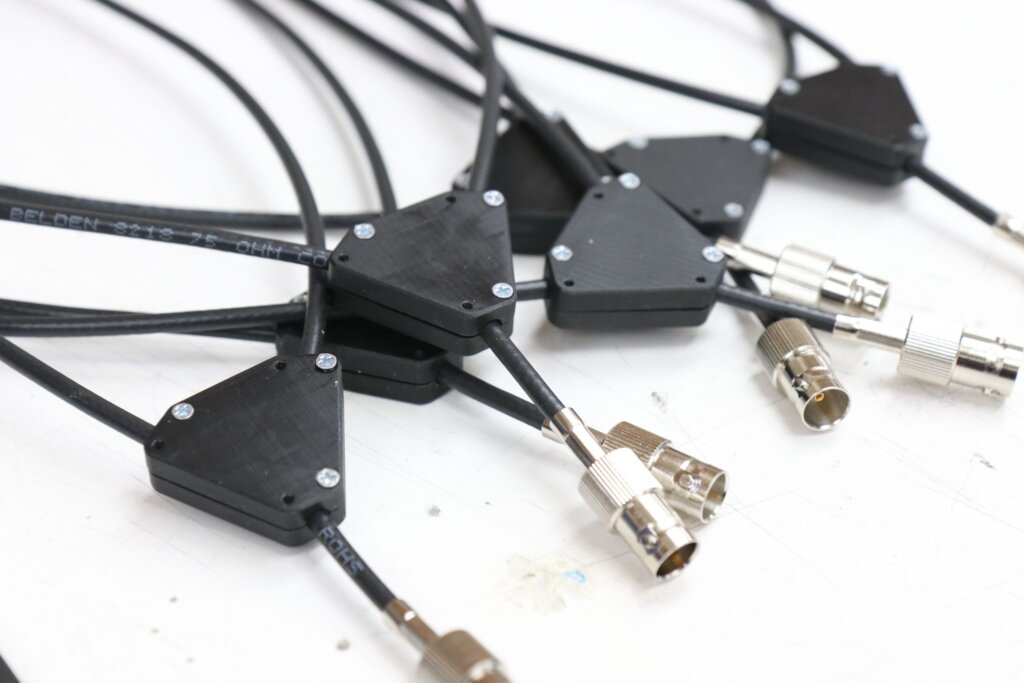
Seals and connectors
It is crucial to choose the proper seal for your cable wisely as well as communicate what that proper seal is to who is assembling the cable harness. Cable seals are dependent on the wires’ gauge, insulation thickness, and terminal plating, so it’s vital to consider the final size of the cable before selecting a seal. Beyond seals, there are a number of additional tools for the ends of a cable that need to be chosen and specified, such as backshells, caps, plugs, and strain reliefs.
Parts considerations
Clients often use their own part numbers when designing cable harnesses, but once a cable manufacturer is involved, it is imperative that there is a legend provided so that they can cross-reference back to the manufacturer part number. If a part does not need to be a specific brand or type, it’s helpful to note “or similar” in the parts list. That way the manufacturer can substitute that part with one that could enhance quality, cost or manufacturing time.
Drawing/part list compatibility
Similar to parts considerations, double checking that the parts listed on the bill of material match the drawing and vice-versa is important. Situations have occurred where a placeholder part or a holdover from a previous revision have been left on one document, so checking against the various documents is always recommended.
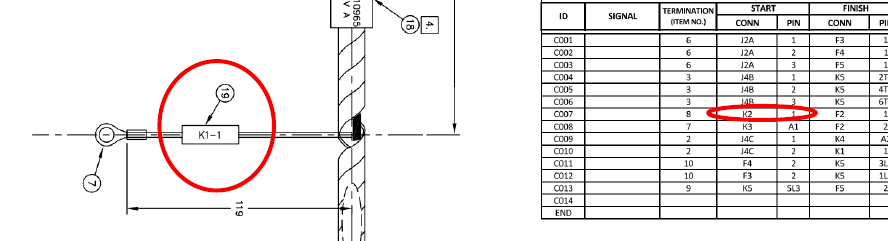
Pin and connector compatibility
At iRex, we understand that the cable harness is a vital part of a larger picture. To that end, we realize how necessary it is that the pin and connectors are compatible not only within the harness itself, but with the terminals that lead to the overall assembly. What makes this more difficult is the fact any discrepancies won’t be noticeable from the cable drawing alone, making it even more important to communicate clearly and proactively with the cable manufacturer.
Environmental considerations
An OEM will have likely already considered the environment their cable will be living in when selecting the components for the cable, but it is also worth considering how the cable assembly as a whole will perform under extreme conditions. Performance issues can arise if a high-mobility application will cause friction and stress between cables or if a high heat environment will cause expansion-related problems.
Testing
There are a range of environmental tests and mechanical tests that can be run on your harness, depending on the use case. Of course, these are in addition to the range of tests already conducted by iRex as part of our commitment to quality assurance. These tests, such as continuity testing, form a base for any cable but if additional testing is needed – like high voltage testing – those needs should be communicated as well.