The Power of Split Sleeves
Trevor Hendricks2024-06-11T21:12:29+00:00Challenge
A cable harness from a client in the automotive industry had a complex cable harness with an extensive variety of terminations needed. They also had a strict timeline for completing the build.
Solution
The original design called for nearly 30 different cables to be pulled through non split tubing and then terminated. When the project made it to iRex, we proposed that the cable be made with a split sleeve so that multiple teams could terminate in batches before the cable harness was sleeved. This way, multiple teams could be specialized on different parts of the cable before it was brought all together, saving both time and cost.
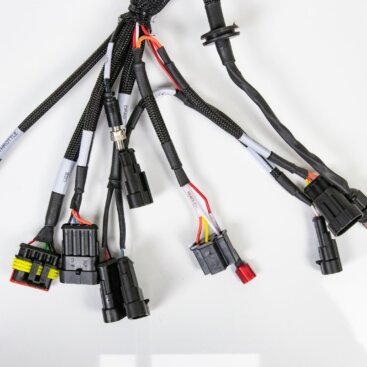
Results
Being able to have teams focus on specific terminations improved consistency and greatly increased throughput. Through this one assembly process change, iRex saved over 1,000 man hours over the course of the project, lowering costs and meeting the tight timeline. To learn more about how iRex introduces small changes for big effects, contact us today.