Tried, True and Old Fashioned: How iRex Uses Cable Boards
Trevor Hendricks2024-06-28T21:54:24+00:00Using cable boards may be the old-fashioned way of assembling cables but with over 20 years of demonstrated experience and a library of wire harness knowledge, our efficiency in cable production and quality check procedures outmatch inexperienced competition that rely on flashy alternative methods.
What is a Cable Board?
A cable board, often called a “nailboard” refers to a mapped-out surface marked with symbols and instructions that lay out the necessary steps to assemble complex cable assemblies. It includes where components and wires need to be placed, the desired cable orientation and direction, where breakouts should occur, where tie wraps need to be affixed, etc. Cable boards serve as a second-step prototyping tool and a template that’s used to ensure each assembly in a purchase order is produced the exact same way.
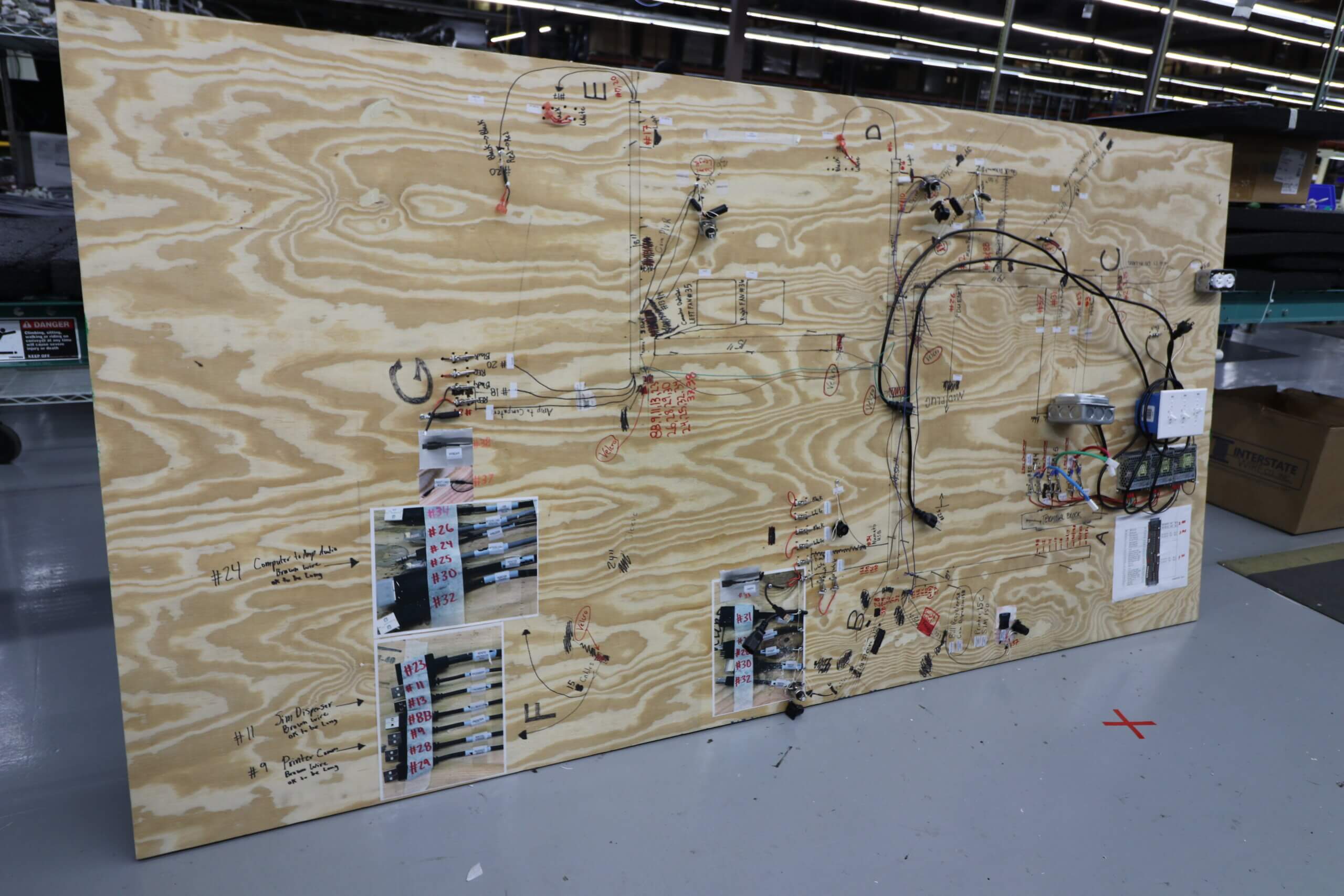
How is it Made?
Cable boards are typically made of 4×8 feet sheets of plywood or pegboard that can be cut down to size, or extended to accommodate larger builds. Our team once utilized our vast production space to construct a 20 foot long cable board to meet the needs of a large-scale project!
Once a cable assembly has been designed, the engineering team will recreate the CAD drawing on the board. Nails (or pegs) are driven into the board to help keep cables in place and set their direction. Inscriptions are etched to guide production.
During this planning phase, cable considerations are important. Engineers should think through distance, heat sink and structural organization. It’s also important to remember that the first build will set the precedent for all other pieces within the order making it crucial for designers to think with manufacturability in mind.
Manufacturers will typically provide their Bill of Materials (BOM) before a project launch. If a client doesn’t send a BOM, our procurement and engineering teams are well-versed in building a list of materials from scratch!
Once a BOM is drafted, it’s attached to the cable board to keep track of part numbers and needed components. Cable engineers might also develop a unique legend of symbols to add to the board. Step-by-steps, detailed procedures or keywords in multiple languages can also be incorporated. How engineers communicate their board’s instructions is their choice entirely, but the goals for cable board design are efficiency, clarity and repeatability.
Considerations During Production
Once the nails are in place and the instructions mapped out, the assembly process begins by placing individual wires onto the board in their corresponding positions. Tie wraps are used to bundle sections of the completed harness to reduce slack and give the harness a malleable shape. Certain builds may require a surplus of tie wraps meaning more time will be spent on the build. Spreading tie wrap locations farther apart can boost production speed and reduce material cost.
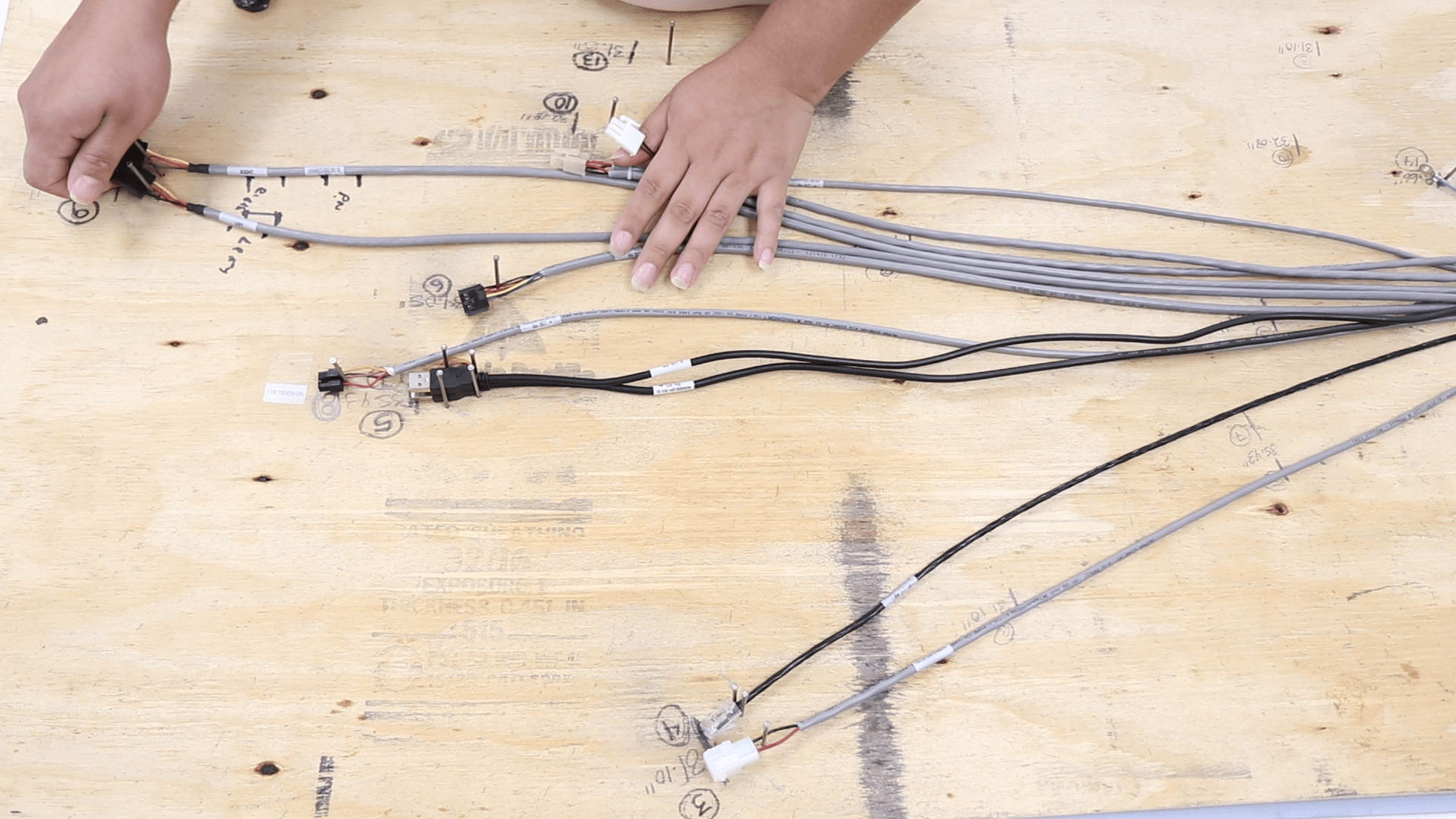
Production technicians will begin fitting cables to the board and then cut the sleeves and fashion wires. The team will also connect cables to separate components and subassemblies. For larger or more complex assemblies, we develop separate cable boards to build and test subassemblies to be inserted in the larger build.
When working with a kiosk manufacturer on a custom order, we separated a top build, or main harness into 31 sub-assemblies. Each sub-assembly was produced and tested individually and then reintroduced to the main harness to finish the project. Since only a certain number of production technicians can operate on a board simultaneously, we divided the project into multiple teams of technicians, expediting the manufacturing process.
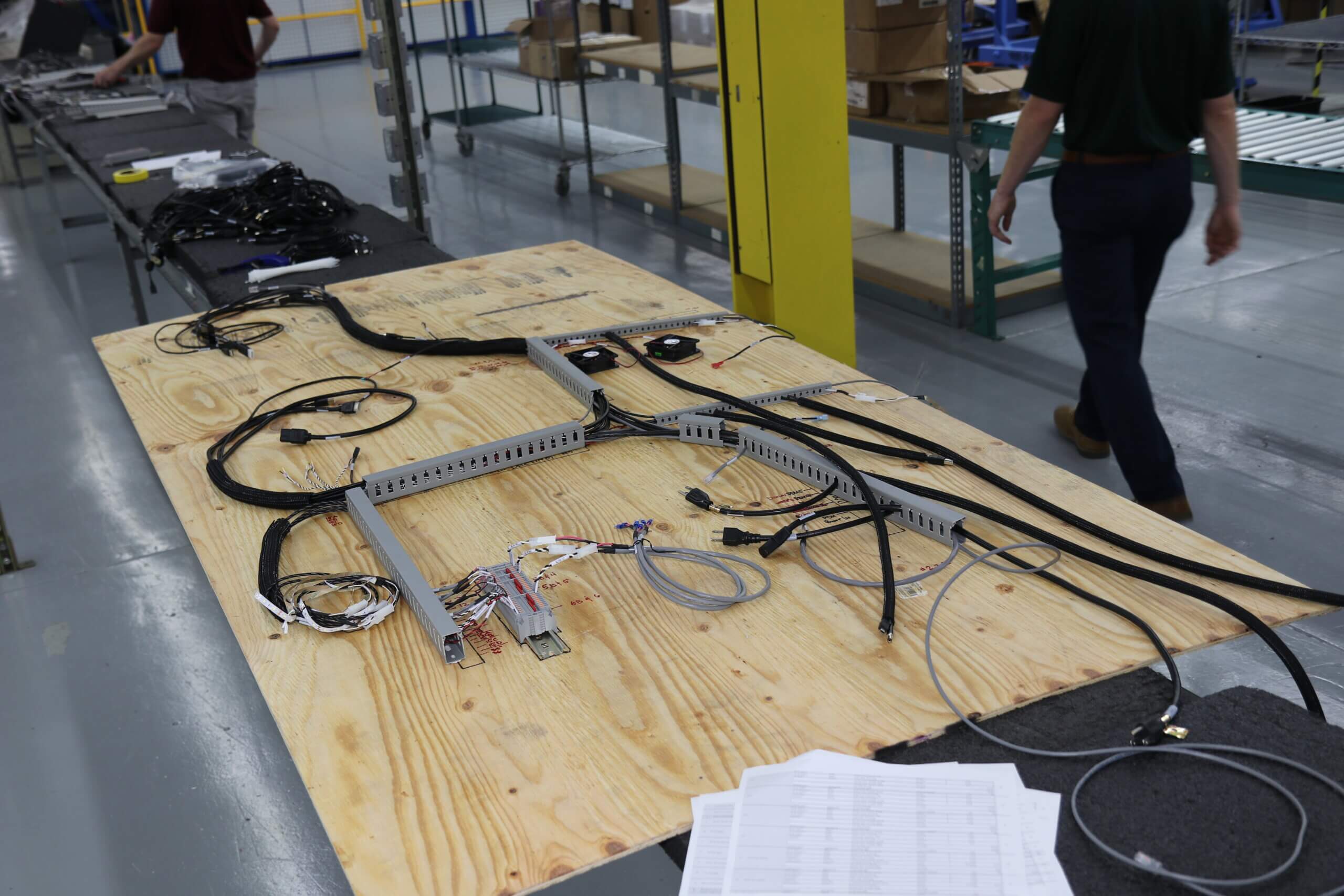
Quality, Inspection and Final Steps
An essential measure iRex takes to provide reliable assemblies is thorough cable testing. While the assembly is on the board, our team will test and inspect each wire, part and connector at each assembly stage. This way, if an error is detected, we can easily single out and replace a malfunctioning piece before it’s inserted into the final product. Once the cable assembly is completed, our team will conduct a final round of testing on a test board before shipping it out or directly installing it into the electronic device.
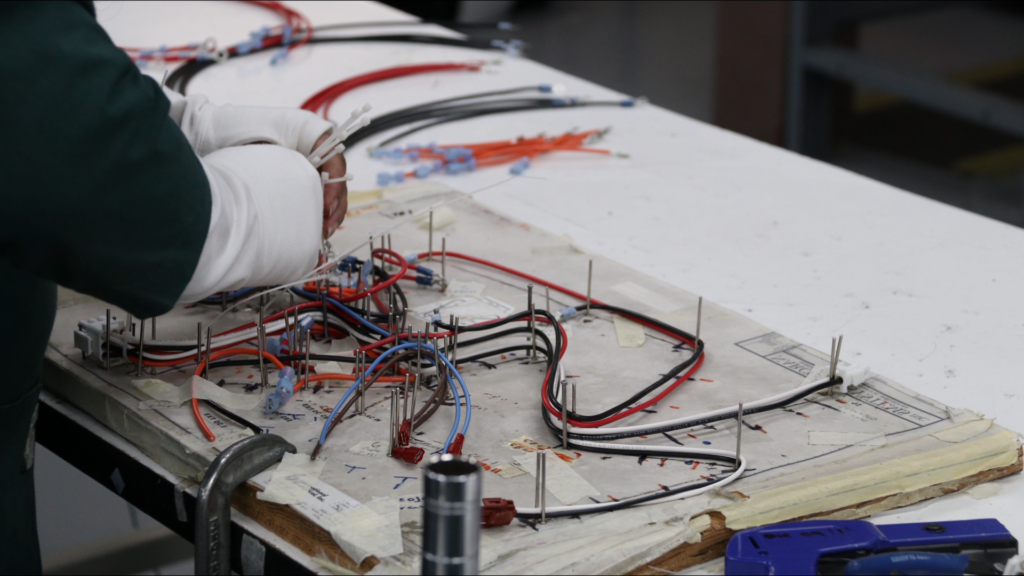
Benefits of Partnering with a Cable Manufacturer
All the units have been produced, tested, packed and shipped out the door – the project is complete! What happens now to the cable board(s) left over? While the materials are cheap enough to discard and replace for the next project, we have found a path of reusability that saves our customers money, drastically reduces startup time and strengthens client relationships.
Our warehousing space allows us to archive used cable boards so that previous projects can be quickly put back into production when a client is ready to reorder or make editable revisions to the original build. For saved projects that have remained on the shelf for years, we digitally preserve the original drawing and seamlessly recycle the board for incoming projects.
Conclusion
Cable boards are a tried and true method of harness assembly. Their implementation is widely considered a common practice among cable houses. We understand that leading an industry takes more than hammering nails into sheets of plywood. It takes a talented workforce that understands the fundamentals of the parts, equipment and products they operate with daily. It also takes a serious commitment to quality and a passion for product development.
We often receive compliments on the organization and speed of our production lines and our extensive quality management systems from existing and prospective customers who tour our facility and see firsthand the care we put into each cable order.
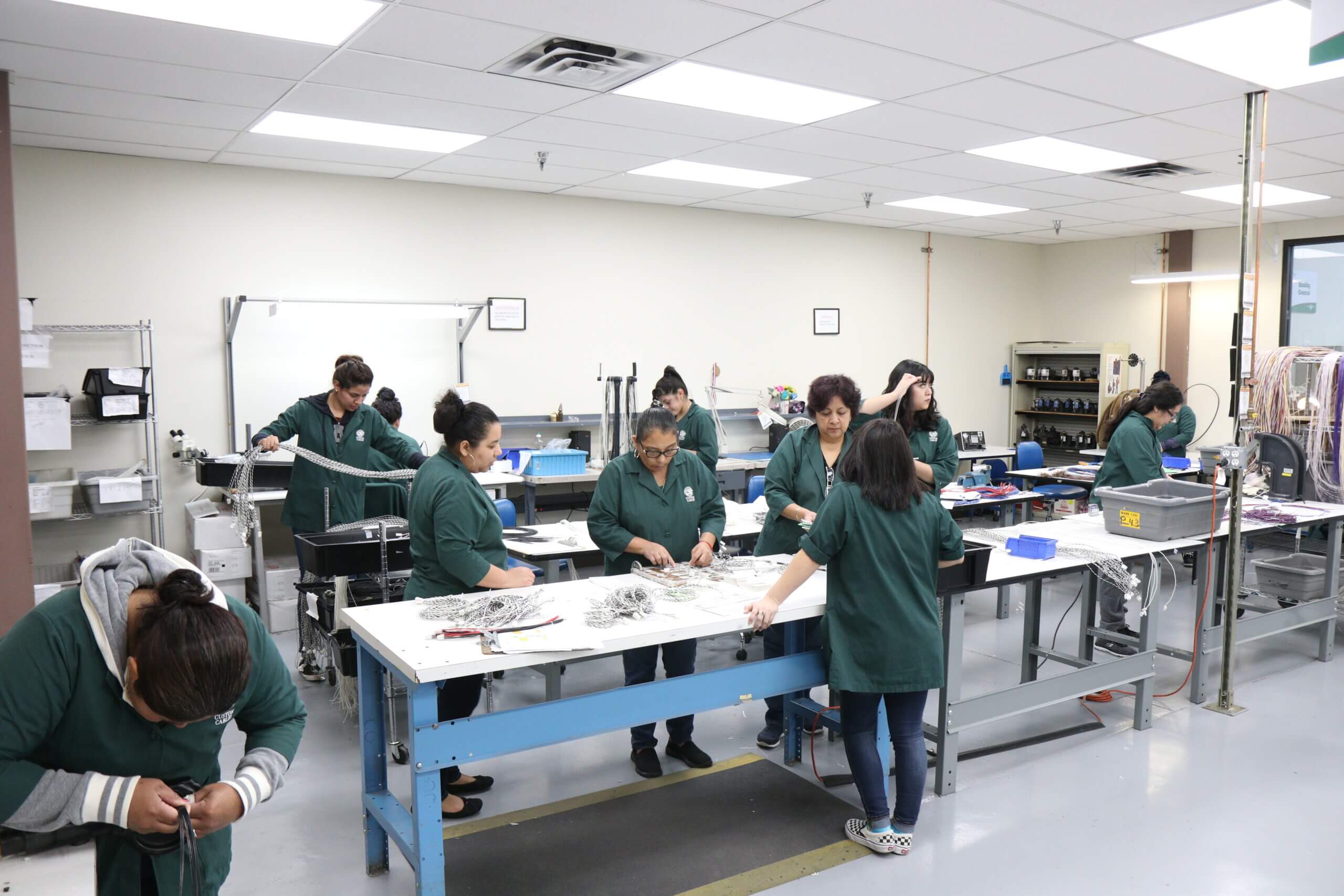
Interested in seeing what we can do for your product line? Reach out today and we’ll set up a personalized facility tour for your team to see how iRex delivers on price, time and quality.