Why Pull Test Your Crimps?
Trevor Hendricks2024-06-11T21:12:53+00:00As discussed in previous articles, crimp joints are an essential component to many cable assemblies. In order to ensure effective crimps, proper crimping force must be used that establishes good metal-to-metal contact. When not enough force is applied, “undercrimping” can leave voids between the wire and the crimp. These voids can diminish conductivity and allow the crimp to be easily removed. When too much force is applied, it’s known as “overcrimping” and failure can occur due to increased resistance in the wire because there’s less conductive area for electrical currents to pass through as well as causing breaks, opens or cracks which can also lead to failures.
Pull-testing, or wire pull testing, is about tensile strength – the resistance to breaking of a material under tension. It is the most basic type of wire bond testing.
If you have a new design with an unusual or an unfamiliar crimp style or are unsure if you’ve selected the optimal gauge wire for the crimp you’re using, pull test. Wire pull testing can be destructive (failure) or non-destructive. Destructive wire pull tests are used for process setups. Non-destructive testing (NDT) is used for the in-line testing of high-reliability applications.
Here are 5 reasons why you should pull test your cable crimp joints:
- Ensures good electrical conductivity (metal-to-metal contact) preventing poor electrical connection
- Measures mechanical strength of connection
- Prevents rework of product, saving money and reducing scrap
- Protects against catastrophic failures
- Repeatable test ensures proper calibration of crimping equipment
At iRex, we perform these tests with the help of Austin Reliability Labs, a fellow member of the TyRex Technology Family. Having the right equipment is the only way to ensure a constant rate of pull, which is why we leverage our Mesur Mark-10 Tensile Tester to perform these ‘Pull and Break’ tests. The readouts from these tests are then compared to a table of minimum pull forces in a manufacturer’s standard or IPC/WHMA A-620 to determine whether the assembly can withstand an adequate amount of stress.
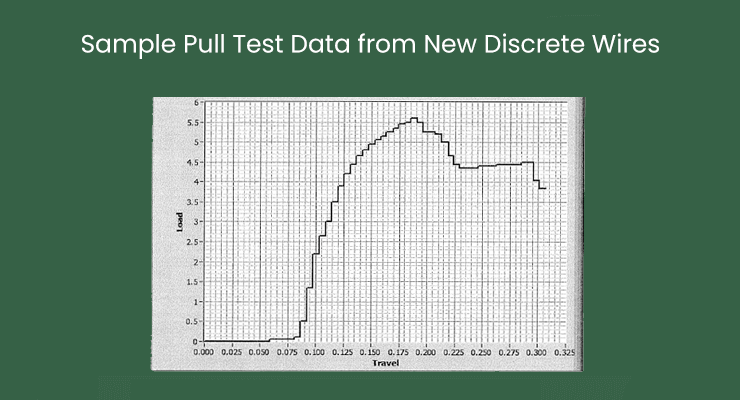
REAL SOLAR CLIENT UTILIZES PULL TESTING in order to ensure unusual and unfamiliar crimp shapes will function when pulled by deer wandering through the solar field. The deer create strain on wires by chewing on them. Austin Reliability Lab ensures that both the deer and the expensive electronic equipment are safe while maintaining safety and functionality throughout operation.
We also recommend that pull tests be used in conjunction with other tests depending on the application of your assembly. Avoid failure in the field with a complete set of environmental tests that replicate the conditions your product might find itself in, like extreme environments and fluctuating temperatures. For more information on iRex’s quality control capabilities, visit this link and be sure to visit our sister company, Austin Reliability Labs, to see an extensive list of all the testing we can provide.